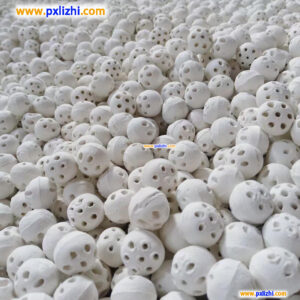
# Alumina Ceramic Ball: Properties and Applications
## Introduction to Alumina Ceramic Balls
Alumina ceramic balls are high-performance industrial components made from aluminum oxide (Al₂O₃). These precision spheres have become essential in various industries due to their exceptional mechanical, thermal, and chemical properties. With alumina content typically ranging from 90% to 99.9%, these ceramic balls offer superior performance compared to traditional metal balls in many applications.
## Key Properties of Alumina Ceramic Balls
### 1. Exceptional Hardness and Wear Resistance
Alumina ceramic balls boast a Mohs hardness of 9, second only to diamond. This makes them highly resistant to wear and abrasion, significantly outperforming steel balls in many applications. Their superior hardness translates to longer service life and reduced maintenance costs.
### 2. High Temperature Stability
These ceramic balls maintain their structural integrity at temperatures up to 1600°C (2912°F), making them ideal for high-temperature applications where metal balls would deform or melt. Their low thermal expansion coefficient ensures dimensional stability across wide temperature ranges.
### 3. Excellent Chemical Resistance
Alumina ceramic balls demonstrate remarkable resistance to acids, alkalis, and organic solvents. They are inert to most chemicals except hydrofluoric acid and strong alkalis at elevated temperatures, making them suitable for corrosive environments.
### 4. Electrical Insulation Properties
With high dielectric strength and volume resistivity, alumina ceramic balls serve as excellent electrical insulators. This property is particularly valuable in electrical and electronic applications where conductivity must be avoided.
### 5. Low Density
Compared to metal alternatives, alumina ceramic balls have a lower density (typically 3.6-3.9 g/cm³), which reduces centrifugal forces in high-speed applications and lowers energy consumption.
## Common Applications of Alumina Ceramic Balls
### 1. Bearings and Precision Components
Alumina ceramic balls are widely used in high-performance bearings for applications requiring:
– Corrosion resistance
– High-speed operation
– Non-magnetic properties
– Electrical insulation
– Extreme temperature stability
### 2. Grinding and Milling Media
In the pharmaceutical, paint, and ceramic industries, alumina balls serve as grinding media due to their:
– High wear resistance
– Chemical inertness
– Contamination-free grinding
– Consistent particle size reduction
Keyword: alumina ceramic ball
### 3. Valve Components
The chemical and petrochemical industries utilize alumina ceramic balls in valves for their:
– Resistance to corrosive fluids
– Ability to withstand high pressures
– Long service life in abrasive environments
### 4. Electronics and Semiconductor Industry
Alumina ceramic balls find applications in electronics as:
– Insulating spacers
– Precision positioning elements
– Components in high-frequency devices
– Semiconductor processing equipment
### 5. Other Specialized Applications
Additional uses include:
– Ball check valves in pumps
– Flow control devices
– Aerospace components
– Nuclear industry applications
– High-temperature furnace components
## Selection Considerations
When choosing alumina ceramic balls for specific applications, consider these factors:
– Alumina content (90%, 95%, 99%, or 99.9%)
– Ball diameter and dimensional tolerances
– Surface finish requirements
– Operating temperature range
– Chemical exposure
– Mechanical load requirements
## Conclusion
Alumina ceramic balls offer a unique combination of properties that make them indispensable in many industrial and technological applications. Their superior hardness, chemical resistance, thermal stability, and electrical insulation characteristics provide significant advantages over traditional metal balls in demanding environments. As material science continues to advance, we can expect even broader applications for these versatile ceramic components in emerging technologies and industries.