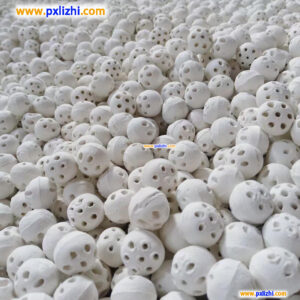
# Alumina Ceramic Ball: Properties and Applications
## Introduction to Alumina Ceramic Balls
Alumina ceramic balls are high-performance ceramic components made from aluminum oxide (Al₂O₃). These precision-engineered spheres have become essential in various industrial applications due to their exceptional mechanical, thermal, and chemical properties. With alumina content typically ranging from 90% to 99.9%, these ceramic balls offer superior performance compared to traditional metal or polymer alternatives.
## Key Properties of Alumina Ceramic Balls
### 1. Exceptional Hardness and Wear Resistance
Alumina ceramic balls boast a Mohs hardness of 9, second only to diamond. This extreme hardness makes them highly resistant to wear, even under continuous friction and high-load conditions. Their wear resistance is approximately 100 times greater than that of steel, ensuring long service life in abrasive environments.
### 2. Outstanding Thermal Stability
These ceramic balls maintain their structural integrity at temperatures up to 1,600°C (2,912°F). Their low thermal expansion coefficient (8×10⁻⁶/°C) prevents dimensional changes during temperature fluctuations, making them ideal for high-temperature applications.
### 3. Excellent Chemical Resistance
Alumina ceramic balls demonstrate remarkable resistance to most acids, alkalis, and organic solvents. They remain unaffected by corrosive environments that would rapidly degrade metal components, ensuring reliable performance in chemical processing applications.
### 4. Electrical Insulation Properties
With high electrical resistivity (10¹⁴ Ω·cm at room temperature), alumina ceramic balls serve as excellent insulators in electrical applications. This property makes them valuable in electronic components and high-voltage equipment.
### 5. Low Density and High Strength
Despite their impressive mechanical properties, alumina ceramic balls have a relatively low density (3.6-3.9 g/cm³), about half that of steel. Their high compressive strength (2,000-4,000 MPa) allows them to withstand significant loads without deformation.
## Common Applications of Alumina Ceramic Balls
### 1. Bearings and Mechanical Components
Alumina ceramic balls are widely used in precision bearings for high-speed applications where traditional steel balls would fail due to heat generation or corrosion. Their use in bearings significantly reduces friction, extends service life, and eliminates the need for lubrication in many cases.
### 2. Grinding and Milling Media
In the mining and pharmaceutical industries, alumina ceramic balls serve as grinding media in ball mills. Their hardness and wear resistance make them ideal for reducing particle size while minimizing contamination of the processed materials.
### 3. Valve Components
The chemical resistance and durability of alumina ceramic balls make them perfect for use in valves handling corrosive fluids or operating in extreme environments. They’re particularly common in the petrochemical and semiconductor industries.
### 4. Electronics and Semiconductor Industry
Keyword: alumina ceramic ball
Alumina ceramic balls find applications in electronic components as insulators, substrates, and in wafer handling systems. Their electrical properties and cleanliness make them essential in semiconductor manufacturing processes.
### 5. Medical and Dental Applications
In the medical field, alumina ceramic balls are used in prosthetic joints and dental implants due to their biocompatibility, wear resistance, and ability to maintain smooth surfaces over time.
## Manufacturing Process
The production of alumina ceramic balls involves several precise steps:
1. Powder preparation and mixing
2. Forming (typically through isostatic pressing)
3. High-temperature sintering (1,500-1,800°C)
4. Precision grinding and polishing
5. Quality inspection and testing
Advanced manufacturing techniques ensure tight dimensional tolerances (often within ±0.001 mm) and superior surface finishes (Ra < 0.02 μm).
## Conclusion
Alumina ceramic balls represent a remarkable fusion of material science and engineering, offering solutions to challenging industrial problems across multiple sectors. Their unique combination of properties – hardness, thermal stability, chemical resistance, and electrical insulation – makes them indispensable in applications where conventional materials fail.