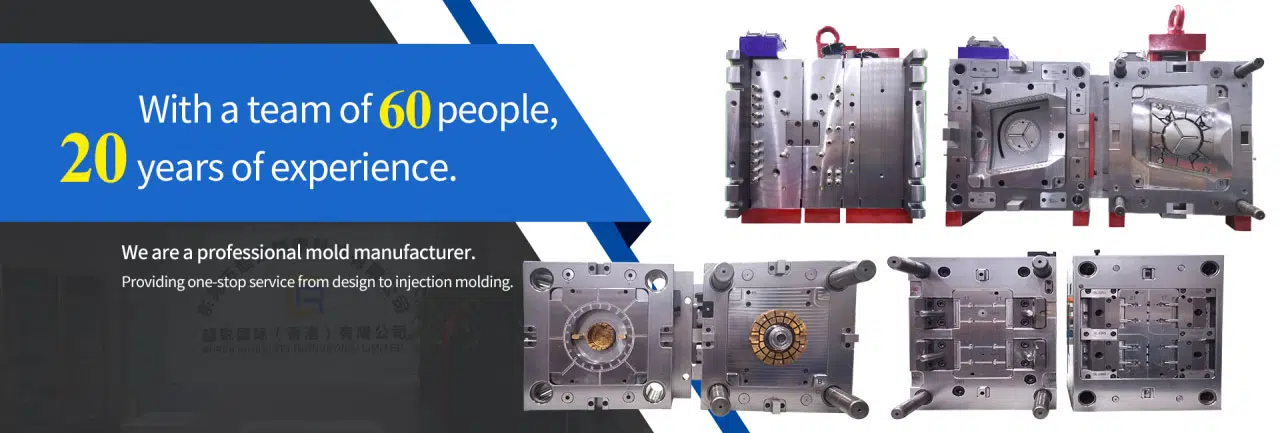
,文章字数在1000字左右
html
Inspection Equipment for Quality Control
Quality control is a critical aspect of manufacturing and production processes across industries. To ensure products meet the required standards, businesses rely on advanced inspection equipment. These tools help detect defects, measure dimensions, and verify compliance with specifications, ultimately enhancing product reliability and customer satisfaction.
Types of Inspection Equipment
Inspection equipment comes in various forms, each designed for specific applications. Here are some of the most commonly used types:
1. Optical Comparators
Optical comparators use magnification and projection to compare a part’s dimensions against a standard template. They are ideal for inspecting complex geometries and small components, providing precise measurements without physical contact.
2. Coordinate Measuring Machines (CMMs)
CMMs are highly accurate devices that measure the physical geometry of objects using a probing system. They are widely used in automotive, aerospace, and medical industries for dimensional analysis and quality assurance.
3. Vision Inspection Systems
Automated vision systems use cameras and software to inspect products for defects, alignment, and surface finish. These systems are essential in high-speed production lines where manual inspection would be impractical.
4. Ultrasonic Testing Equipment
Ultrasonic testing devices use high-frequency sound waves to detect internal flaws in materials. They are commonly used in welding, casting, and composite material inspections.
5. Hardness Testers
These instruments measure a material’s resistance to deformation, which is crucial for determining product durability. Different methods like Rockwell, Brinell, and Vickers are used depending on material properties.
Benefits of Using Inspection Equipment
Implementing proper inspection equipment offers numerous advantages for manufacturers:
- Improved Accuracy: Automated systems eliminate human error in measurements and defect detection.
- Increased Efficiency: High-speed inspection systems can process hundreds of parts per minute.
- Cost Reduction: Early defect detection prevents waste and reduces rework expenses.
- Consistency: Equipment provides uniform inspection standards across production batches.
- Documentation: Digital systems automatically record inspection data for traceability.
Keyword: Inspection Equipment
Choosing the Right Inspection Equipment
Selecting appropriate inspection equipment requires careful consideration of several factors:
1. Application Requirements
Determine what characteristics need inspection (dimensions, surface defects, material properties) and the required precision level.
2. Production Volume
High-volume production may require automated systems, while low-volume operations might benefit from manual or semi-automatic equipment.
3. Material Characteristics
Consider whether the material is metallic, plastic, transparent, or reflective, as this affects the choice of inspection technology.
4. Environmental Conditions
Some equipment may require controlled environments (temperature, humidity, vibration-free) for optimal performance.
5. Budget Constraints
Balance initial investment costs with long-term benefits like labor savings and quality improvements.
Emerging Trends in Inspection Technology
The field of quality inspection is constantly evolving with technological advancements:
1. Artificial Intelligence Integration
AI-powered systems can learn from inspection data to improve defect recognition and reduce false positives over time.