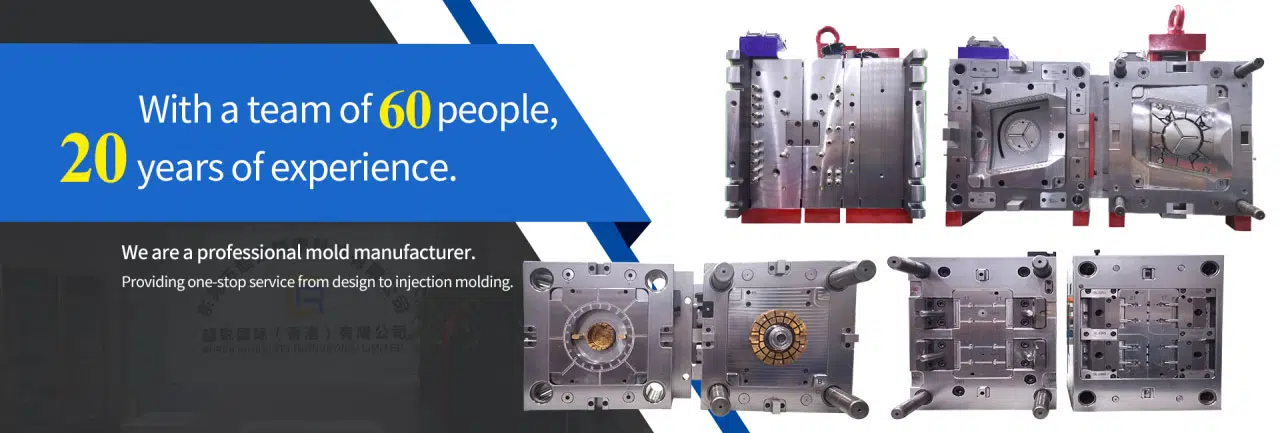
# Digital Manufacturing: Revolutionizing Modern Production Processes
## The Rise of Digital Manufacturing
Digital manufacturing represents a transformative approach to modern production processes. By integrating advanced technologies with traditional manufacturing methods, companies are achieving unprecedented levels of efficiency, precision, and flexibility. This paradigm shift is reshaping industries across the globe, from automotive to aerospace, and from consumer electronics to medical devices.
At its core, digital manufacturing leverages computer-based systems to create, simulate, analyze, and optimize production processes before physical implementation. This digital-first approach minimizes waste, reduces costs, and accelerates time-to-market for new products.
## Key Technologies Driving Digital Manufacturing
Several cutting-edge technologies form the foundation of digital manufacturing:
### 1. Industrial Internet of Things (IIoT)
Connected sensors and devices throughout the manufacturing environment collect real-time data, enabling predictive maintenance and process optimization.
### 2. Additive Manufacturing (3D Printing)
This technology allows for rapid prototyping and production of complex geometries that would be impossible or prohibitively expensive with traditional methods.
### 3. Digital Twins
Virtual replicas of physical assets enable simulation and analysis of performance under various conditions without disrupting actual operations.
### 4. Artificial Intelligence and Machine Learning
AI algorithms analyze vast amounts of production data to identify patterns, predict outcomes, and optimize processes autonomously.
## Benefits of Digital Manufacturing
The adoption of digital manufacturing offers numerous advantages:
• Increased Efficiency: Automated processes and real-time monitoring reduce downtime and improve resource utilization.
• Enhanced Quality: Continuous data collection and analysis enable immediate detection and correction of defects.
• Greater Flexibility: Digital systems can quickly adapt to design changes or new product introductions.
• Sustainability: Optimized processes reduce material waste and energy consumption.
• Improved Safety: Digital simulations identify potential hazards before they occur in the physical environment.
## Challenges in Implementation
While the benefits are substantial, organizations face several challenges when transitioning to digital manufacturing:
1. High Initial Investment
The cost of implementing advanced technologies and training personnel can be significant, particularly for small and medium-sized enterprises.
2. Cybersecurity Risks
Increased connectivity creates vulnerabilities that require robust security measures to protect sensitive data and operations.
Keyword: Digital Manufacturing
3. Workforce Transformation
The shift to digital manufacturing demands new skill sets, necessitating comprehensive training programs and cultural adaptation.
4. Data Integration
Combining legacy systems with new digital platforms often presents technical and organizational challenges.
## The Future of Digital Manufacturing
As technology continues to evolve, digital manufacturing will become increasingly sophisticated. Emerging trends include:
- Wider adoption of 5G networks for faster, more reliable connectivity
- Expansion of edge computing for real-time data processing
- Integration of augmented reality for maintenance and training
- Development of more advanced materials for additive manufacturing
- Greater emphasis on sustainable and circular production models
## Conclusion
Digital manufacturing is not merely an incremental improvement to traditional methods—it represents a fundamental reimagining of how products are designed, produced, and maintained. As organizations navigate the challenges of implementation, those who successfully embrace this transformation will gain significant competitive advantages in efficiency, innovation, and responsiveness to market demands. The future of manufacturing is digital, and the revolution is well underway.