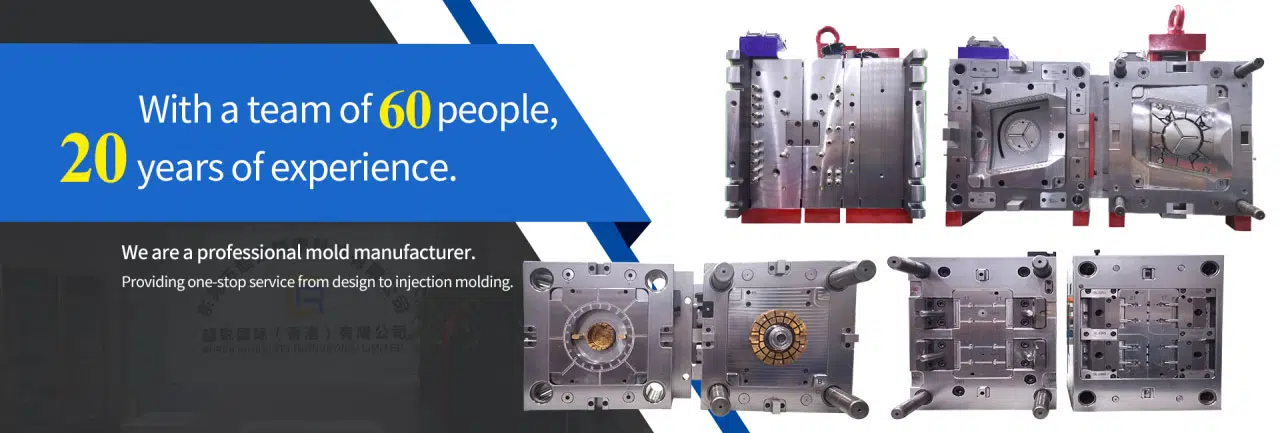
# Die Casting Process and Applications
## What is Die Casting?
Die casting is a metal casting process that involves forcing molten metal under high pressure into a mold cavity. The mold cavity is created using two hardened tool steel dies which have been machined into shape and work similarly to an injection mold during the process.
## The Die Casting Process
The die casting process consists of five main steps:
### 1. Clamping
The first step is the preparation and clamping of the two halves of the die. Each die half is cleaned and lubricated to facilitate both the casting process and the removal of the finished part.
### 2. Injection
Molten metal is then injected into the die under high pressure. The high pressure ensures the metal fills the entire die cavity, including all thin sections and complex geometries.
### 3. Cooling
The molten metal is allowed to cool and solidify in the die. The cooling time depends on the type of metal and the thickness of the casting.
### 4. Ejection
After the cooling period, the die halves are opened and the casting is ejected by the ejector pins.
### 5. Trimming
During cooling, excess material may form at the parting line, around the ejector pins, and at any overflow locations. This excess material is trimmed from the casting either manually or using a trimming press.
## Types of Die Casting
There are two main types of die casting:
### Hot-Chamber Die Casting
This process is primarily used for metals with low melting points such as zinc, magnesium, and lead alloys. The injection mechanism is immersed in the molten metal bath.
### Cold-Chamber Die Casting
This method is used for metals with high melting points like aluminum and copper alloys. The molten metal is ladled into the cold chamber for each shot.
## Materials Used in Die Casting
Common materials used in die casting include:
– Aluminum alloys
– Zinc alloys
– Magnesium alloys
– Copper alloys
– Lead and tin alloys (less common)
## Advantages of Die Casting
Die casting offers numerous benefits:
– High production rates
– Excellent dimensional accuracy
– Smooth cast surfaces
– Thin walls can be cast
– Minimal machining required
– Long mold life
– Ability to cast complex shapes
## Applications of Die Casting
Die cast parts are used in a wide variety of applications across many industries:
### Automotive Industry
– Engine blocks
– Transmission cases
– Cylinder heads
– Wheels
– Bracket components
### Consumer Electronics
– Laptop and tablet cases
– Smartphone components
– Camera bodies
– Speaker housings
### Industrial Equipment
– Pump housings
– Valve bodies
– Power tool components
– Hydraulic cylinders
### Household Items
– Door handles
– Faucet parts
– Appliance components
– Lighting fixtures
## Future of Die Casting
The die casting industry continues to evolve with advancements in:
– New alloy development
– Improved die materials
– Computer-aided design and simulation
– Automation in production
Keyword: Die Casting
– Environmentally friendly processes
As manufacturing demands grow for lightweight, durable components, die casting remains a vital process for producing high-quality metal parts efficiently and cost-effectively.