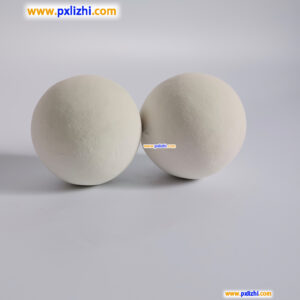
# Inert Ceramic Ball Applications in Industrial Processes
## Introduction to Inert Ceramic Balls
Inert ceramic balls are high-quality, chemically stable ceramic spheres used in various industrial applications. These balls are manufactured from high-purity alumina or other ceramic materials, offering exceptional resistance to thermal shock, chemical corrosion, and mechanical wear.
## Key Properties of Inert Ceramic Balls
Keyword: inert ceramic ball
The unique characteristics of inert ceramic balls make them indispensable in industrial settings:
– High temperature resistance (up to 1600°C)
– Excellent chemical inertness
– Superior mechanical strength
– Low water absorption
– Thermal shock resistance
– Customizable sizes and compositions
## Primary Industrial Applications
### 1. Petrochemical Industry
Inert ceramic balls serve as catalyst supports and tower packing in petroleum refining processes. They help distribute liquids evenly and prevent catalyst bed compaction in:
– Fluid catalytic cracking (FCC) units
– Hydroprocessing reactors
– Reforming units
– Isomerization processes
### 2. Chemical Processing
Chemical manufacturers utilize inert ceramic balls for:
– Protecting catalyst beds from contamination
– Supporting fragile catalysts
– Distributing reactants evenly
– Acting as thermal insulators in high-temperature reactions
### 3. Environmental Protection
These ceramic balls play a crucial role in environmental applications:
– Waste gas treatment systems
– Flue gas desulfurization
– VOC (volatile organic compound) removal
– Wastewater treatment processes
### 4. Other Industrial Uses
Additional applications include:
– Heat storage media in thermal systems
– Grinding media in ball mills
– Packing material in distillation columns
– Support media in biological treatment systems
## Advantages Over Alternative Materials
Inert ceramic balls offer several benefits compared to metal or plastic alternatives:
– Longer service life due to wear resistance
– No catalytic side reactions
– Better performance in corrosive environments
– Higher temperature tolerance
– Lower maintenance requirements
## Selection Considerations
When choosing inert ceramic balls for industrial processes, consider:
– Operating temperature range
– Chemical environment
– Mechanical stress requirements
– Size and shape specifications
– Pressure drop considerations
– Cost-effectiveness for the application
## Future Trends
The market for inert ceramic balls continues to grow with:
– Development of advanced ceramic compositions
– Increased demand from emerging economies
– Stricter environmental regulations
– Expansion of petrochemical and chemical industries
– New applications in renewable energy technologies
Inert ceramic balls remain a critical component in numerous industrial processes, offering reliability, durability, and performance advantages that make them the preferred choice for demanding applications across multiple industries.