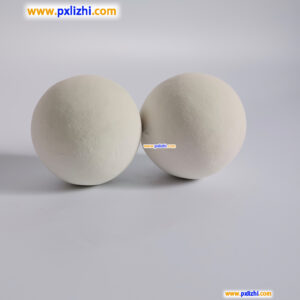
。
# Inert Ceramic Ball Applications in Industrial Processes
## Introduction to Inert Ceramic Balls
Inert ceramic balls are widely used in various industrial processes due to their excellent chemical stability, high mechanical strength, and thermal resistance. These small spherical ceramic pieces play a crucial role in numerous applications across different industries.
Keyword: inert ceramic ball
## Key Properties of Inert Ceramic Balls
The effectiveness of inert ceramic balls stems from their unique properties:
– High chemical inertness
– Exceptional thermal stability
– Superior mechanical strength
– Low water absorption
– Excellent resistance to corrosion
## Major Industrial Applications
### 1. Petrochemical Industry
In the petrochemical sector, inert ceramic balls serve as:
– Catalyst supports in reactors
– Tower packing materials
– Bed support media
– Distributors in fractionation columns
### 2. Chemical Processing
Chemical plants utilize these ceramic balls for:
– Protecting catalyst beds
– Improving gas distribution
– Supporting fragile catalysts
– Preventing clogging in reactors
### 3. Environmental Protection
Environmental applications include:
– Waste gas treatment systems
– Water purification processes
– Flue gas desulfurization
– VOC (Volatile Organic Compounds) removal
### 4. Metallurgical Industry
In metallurgy, inert ceramic balls are used for:
– High-temperature furnace linings
– Metal heat treatment processes
– Molten metal filtration
– Refractory applications
## Benefits of Using Inert Ceramic Balls
The advantages of incorporating inert ceramic balls in industrial processes include:
– Extended equipment lifespan
– Improved process efficiency
– Reduced maintenance costs
– Enhanced product quality
– Better temperature distribution
– Increased surface area for reactions
## Selection Criteria
When choosing inert ceramic balls for specific applications, consider:
– Size and diameter requirements
– Operating temperature range
– Chemical compatibility
– Pressure conditions
– Mechanical load requirements
– Specific surface area needs
## Maintenance and Handling
Proper maintenance ensures optimal performance:
– Regular inspection for cracks or damage
– Proper cleaning procedures
– Correct storage conditions
– Appropriate handling to prevent breakage
– Periodic replacement schedules
## Future Trends
The future of inert ceramic ball technology includes:
– Development of nano-structured ceramic balls
– Improved thermal conductivity variants
– Customized shapes for specific applications
– Enhanced durability formulations
– Smart ceramic balls with embedded sensors
## Conclusion
Inert ceramic balls continue to be indispensable components in numerous industrial processes. Their versatility, durability, and chemical stability make them valuable assets across multiple sectors. As technology advances, we can expect even more innovative applications for these remarkable ceramic components.