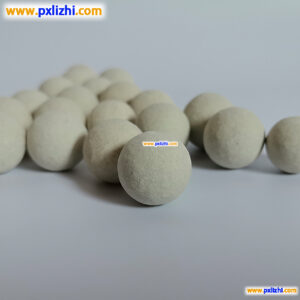
# Ceramic Ball Manufacturing Process and Applications
## Introduction to Ceramic Balls
Ceramic balls are precision-engineered components made from various ceramic materials, offering exceptional properties such as high hardness, wear resistance, and thermal stability. These spherical components find applications across multiple industries due to their superior performance characteristics compared to metal alternatives.
## Manufacturing Process of Ceramic Balls
### 1. Raw Material Selection
The manufacturing process begins with selecting appropriate ceramic materials. Common choices include:
– Alumina (Al2O3)
– Zirconia (ZrO2)
– Silicon nitride (Si3N4)
– Silicon carbide (SiC)
### 2. Powder Preparation
The selected ceramic powder undergoes several preparation steps:
– Milling to achieve uniform particle size
– Mixing with binders and additives
– Spray drying to create free-flowing granules
### 3. Forming Process
Two primary methods are used to form ceramic balls:
Keyword: ceramic ball
#### Isostatic Pressing
Cold isostatic pressing (CIP) applies uniform pressure from all directions to create green bodies with high density and minimal defects.
#### Injection Molding
For complex shapes or small sizes, ceramic injection molding (CIM) offers precise control over dimensions.
### 4. Sintering
The formed green bodies undergo high-temperature sintering:
– Temperatures typically range from 1400°C to 1800°C
– Process duration varies from several hours to days
– Controlled atmosphere (air, vacuum, or specific gas) depending on material
### 5. Precision Grinding
After sintering, balls undergo precision grinding to achieve:
– Tight dimensional tolerances (often within microns)
– Superior surface finish (Ra < 0.02 μm)
– Perfect sphericity (grade 5 or better)
### 6. Quality Control
Rigorous quality checks ensure:
– Dimensional accuracy
– Surface quality
– Mechanical properties
– Batch consistency
## Applications of Ceramic Balls
### Industrial Bearings
Ceramic balls excel in bearing applications due to:
– Higher speed capabilities
– Reduced friction
– Corrosion resistance
– Longer service life
### Valve Components
In severe service valves, ceramic balls provide:
– Exceptional wear resistance
– Chemical inertness
– High temperature stability
### Medical Devices
Biocompatible ceramic balls are used in:
– Orthopedic implants
– Dental applications
– Surgical instruments
### Aerospace and Defense
Critical applications include:
– Guidance systems
– High-performance bearings
– Wear-resistant components
### Electronics and Semiconductors
Ceramic balls serve as:
– Substrates for electronic components
– Insulating elements
– Precision positioning devices
## Advantages Over Metal Balls
Ceramic balls offer several benefits compared to their metal counterparts:
– 60% lighter than steel
– 3-10 times longer service life
– Higher temperature resistance
– Better corrosion resistance
– Non-magnetic properties
– Electrical insulation
## Future Trends in Ceramic Ball Technology
Emerging developments include:
– Nanostructured ceramic materials
– Hybrid ceramic-metal composites
– Additive manufacturing techniques
– Smart ceramics with embedded sensors
As manufacturing processes continue to advance, ceramic balls are finding new applications across industries that demand extreme performance and reliability.