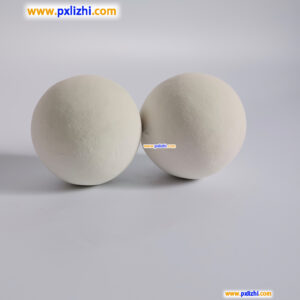
# Inert Ceramic Ball Applications in Industrial Processes
## Introduction to Inert Ceramic Balls
Inert ceramic balls are widely used in various industrial processes due to their excellent chemical stability, high mechanical strength, and thermal resistance. These small spherical ceramic pieces play a crucial role in many chemical and petrochemical applications, serving as catalyst supports, tower packing, and grinding media.
## Key Properties of Inert Ceramic Balls
The effectiveness of inert ceramic balls in industrial applications stems from their unique properties:
– High temperature resistance
– Excellent chemical inertness
– Superior mechanical strength
– Low water absorption
– Uniform size distribution
– Good thermal shock resistance
## Major Industrial Applications
### 1. Catalyst Support in Chemical Reactors
Inert ceramic balls serve as excellent catalyst supports in fixed-bed reactors. They provide a stable platform for active catalysts while ensuring proper gas or liquid distribution throughout the reactor bed. Their thermal stability makes them ideal for high-temperature catalytic processes.
### 2. Tower Packing in Distillation Columns
These ceramic balls are commonly used as tower packing in distillation and absorption columns. They create a large surface area for mass transfer while maintaining low pressure drops, significantly improving separation efficiency in processes like:
– Petroleum refining
– Gas processing
– Chemical production
– Wastewater treatment
### 3. Grinding Media in Ball Mills
Due to their high density and wear resistance, inert ceramic balls are excellent grinding media for ball mills. They are particularly useful in:
Keyword: inert ceramic ball
– Mineral processing
– Paint and pigment production
– Ceramic powder manufacturing
– Pharmaceutical applications
### 4. Heat Exchange Media
Inert ceramic balls serve as heat exchange media in regenerative thermal oxidizers and other heat recovery systems. Their high thermal capacity and resistance to thermal shock make them perfect for storing and transferring heat in industrial processes.
## Advantages Over Alternative Materials
Compared to metal or plastic alternatives, inert ceramic balls offer several distinct advantages:
– Longer service life due to superior wear resistance
– Better performance in corrosive environments
– Higher temperature tolerance
– Lower maintenance requirements
– More consistent performance over time
## Selection Considerations
When choosing inert ceramic balls for industrial applications, several factors should be considered:
– Operating temperature range
– Chemical environment
– Mechanical stress requirements
– Size and shape specifications
– Pressure drop considerations
– Cost-effectiveness
## Future Trends in Inert Ceramic Ball Applications
As industrial processes become more demanding, the development of advanced ceramic materials continues to expand the applications of inert ceramic balls. Emerging trends include:
– Nanostructured ceramic balls for enhanced performance
– Customized formulations for specific industrial applications
– Improved manufacturing techniques for better consistency
– Integration with smart monitoring systems
Inert ceramic balls have become indispensable components in numerous industrial processes, offering reliable performance under challenging conditions. Their versatility, durability, and cost-effectiveness ensure they will remain critical elements in industrial applications for years to come.