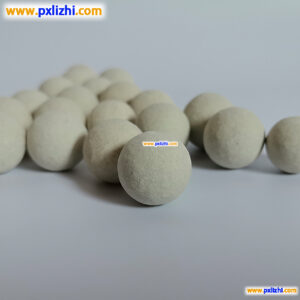
# Ceramic Ball Applications in Industrial Processes
## Introduction to Ceramic Balls
Keyword: ceramic ball
Ceramic balls are highly versatile components used across various industrial applications. These small, spherical objects are made from advanced ceramic materials, offering exceptional properties that make them ideal for demanding environments.
## Key Properties of Ceramic Balls
The widespread use of ceramic balls in industrial processes stems from their unique characteristics:
– High hardness and wear resistance
– Excellent thermal stability
– Superior corrosion resistance
– Low density compared to metal alternatives
– Electrical insulation properties
## Major Industrial Applications
### 1. Bearing Systems
Ceramic balls have revolutionized bearing technology, particularly in high-performance applications. Their use in hybrid bearings (ceramic balls with steel races) provides:
– Reduced friction and heat generation
– Longer service life in contaminated environments
– Higher speed capabilities
– Improved performance in extreme temperatures
### 2. Grinding and Milling
In the mineral processing industry, ceramic balls serve as grinding media in ball mills. Their advantages include:
– Higher grinding efficiency than steel balls
– Reduced contamination of processed materials
– Lower energy consumption
– Minimal wear and longer operational life
### 3. Valve Components
The chemical and petrochemical industries extensively use ceramic balls in valve applications due to:
– Exceptional resistance to corrosive fluids
– Ability to maintain sealing integrity under high pressure
– Reduced maintenance requirements
– Compatibility with aggressive media
### 4. Aerospace and Defense
Ceramic balls find critical applications in aerospace systems, including:
– Guidance system components
– High-performance bearings for jet engines
– Armor systems (as part of composite materials)
– Satellite components requiring dimensional stability
## Emerging Applications
Recent technological advancements have expanded ceramic ball applications into new areas:
– Medical devices and implants
– Semiconductor manufacturing equipment
– Renewable energy systems
– High-precision measurement instruments
## Selection Considerations
When choosing ceramic balls for industrial applications, engineers must consider:
– Material composition (alumina, zirconia, silicon nitride, etc.)
– Size and dimensional tolerances
– Surface finish requirements
– Operating environment (temperature, chemicals, pressure)
– Load and stress conditions
## Future Outlook
The demand for ceramic balls continues to grow as industries seek more efficient, durable, and environmentally friendly solutions. Ongoing material science research promises even better performance characteristics, potentially opening new application areas in advanced manufacturing and energy systems.