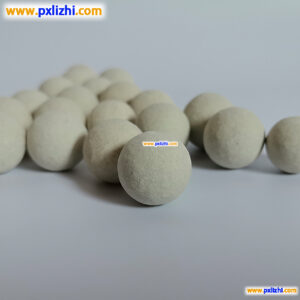
# Ceramic Ball Manufacturing Process and Applications
## Introduction to Ceramic Balls
Ceramic balls are precision-engineered spherical components made from various ceramic materials. These balls offer exceptional properties such as high hardness, wear resistance, chemical inertness, and thermal stability, making them valuable in numerous industrial applications.
## Manufacturing Process of Ceramic Balls
### 1. Raw Material Selection
The manufacturing process begins with selecting appropriate ceramic materials based on the intended application. Common materials include:
– Alumina (Al2O3)
Keyword: ceramic ball
– Zirconia (ZrO2)
– Silicon nitride (Si3N4)
– Silicon carbide (SiC)
### 2. Powder Preparation
The selected ceramic material is ground into fine powder and mixed with binders and additives to improve formability. The powder mixture undergoes:
– Milling to achieve uniform particle size
– Drying to remove moisture
– Sieving to ensure consistent particle distribution
### 3. Forming Process
The prepared powder is shaped into spherical forms using various techniques:
– Isostatic pressing: Powder is compressed in a flexible mold under high pressure
– Extrusion: Material is forced through a die to form cylindrical shapes that are later cut and rounded
– Injection molding: Powder-binder mixture is injected into spherical molds
### 4. Sintering
The formed green balls undergo high-temperature sintering (typically 1400-1800°C) to:
– Remove organic binders
– Densify the ceramic structure
– Achieve final mechanical properties
### 5. Grinding and Polishing
After sintering, the balls undergo precision grinding and polishing to:
– Achieve exact dimensional tolerances
– Improve surface finish
– Meet required sphericity standards
### 6. Quality Control
Each ceramic ball undergoes rigorous testing for:
– Dimensional accuracy
– Surface quality
– Mechanical properties
– Chemical composition
## Applications of Ceramic Balls
### 1. Bearing Applications
Ceramic balls are widely used in high-performance bearings for:
– Aerospace components
– Medical equipment
– High-speed machine tools
– Semiconductor manufacturing
### 2. Valve Components
In industrial valves, ceramic balls provide:
– Excellent wear resistance
– Corrosion protection
– Long service life in abrasive environments
### 3. Grinding Media
Ceramic balls serve as grinding media in:
– Paint and pigment production
– Pharmaceutical manufacturing
– Food processing
– Mineral processing
### 4. Automotive Industry
Applications include:
– Fuel injection systems
– Turbocharger components
– High-temperature sensors
### 5. Other Industrial Uses
– Pump components
– Flow control devices
– Measurement instruments
– Ball screws and linear guides
## Advantages of Ceramic Balls
Ceramic balls offer several benefits over traditional metal balls:
– Higher hardness and wear resistance
– Lower density (reducing centrifugal forces)
– Better corrosion resistance
– Electrical insulation properties
– Non-magnetic characteristics
– Ability to withstand extreme temperatures
## Future Trends in Ceramic Ball Technology
The ceramic ball industry continues to evolve with:
– Development of new ceramic composites
– Improved manufacturing precision
– Expanded applications in renewable energy
– Growing use in medical implants
– Enhanced surface treatment technologies
As technology advances, ceramic balls are expected to play an increasingly important role in various high-performance applications across multiple industries.