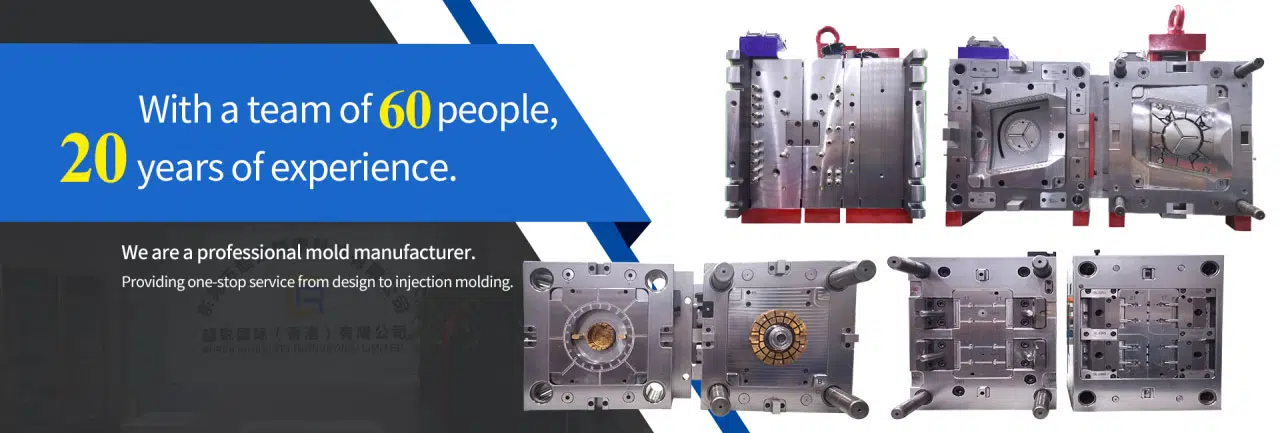
# Injection Molding: Process, Applications, and Advancements
## Introduction to Injection Molding
Injection molding is a manufacturing process widely used for producing plastic parts in large volumes. It involves injecting molten material into a mold where it cools and solidifies into the desired shape. This process is highly efficient and capable of producing complex geometries with excellent precision.
## The Injection Molding Process
The injection molding process consists of several key steps:
### 1. Clamping
The two halves of the mold are securely closed by the clamping unit before injection begins. Proper clamping ensures the mold remains closed during the injection process.
### 2. Injection
Plastic pellets are fed into the machine, melted, and then injected into the mold cavity under high pressure. The material fills the entire cavity, taking the shape of the desired part.
### 3. Cooling
After injection, the molten plastic begins to cool and solidify within the mold. Cooling time varies depending on the material and part thickness.
### 4. Ejection
Once sufficiently cooled, the mold opens and the finished part is ejected using ejector pins. The mold then closes again for the next cycle.
## Materials Used in Injection Molding
A wide variety of thermoplastic materials can be used in injection molding, including:
– Polypropylene (PP)
– Acrylonitrile Butadiene Styrene (ABS)
– Polycarbonate (PC)
Keyword: Injection Molding
– Polyethylene (PE)
– Nylon (PA)
– Thermoplastic elastomers (TPE)
## Applications of Injection Molding
Injection molding finds applications across numerous industries:
### Consumer Products
From toothbrush handles to food containers, injection molding produces countless everyday items.
### Automotive Components
Many automotive parts, including dashboards, bumpers, and interior trim, are manufactured using injection molding.
### Medical Devices
Sterile, precise medical components such as syringes and surgical instruments are often injection molded.
### Electronics
Plastic housings for electronics, connectors, and other components are commonly produced through this process.
## Recent Advancements in Injection Molding Technology
The injection molding industry continues to evolve with new technologies:
### 1. Multi-material Injection Molding
This allows different materials to be combined in a single molding cycle, creating parts with varying properties.
### 2. Micro-injection Molding
Enables production of extremely small, precise components for medical and electronics applications.
### 3. Gas-assisted Injection Molding
Uses inert gas to create hollow sections within parts, reducing weight and material usage.
### 4. Intelligent Molding Systems
Incorporates sensors and AI to monitor and optimize the molding process in real-time.
## Environmental Considerations
Modern injection molding addresses sustainability through:
– Increased use of biodegradable and recycled materials
– Energy-efficient machines
– Reduced material waste through optimized designs
– Closed-loop recycling systems
## Conclusion
Injection molding remains one of the most versatile and efficient manufacturing processes for plastic parts. With continuous technological advancements, it continues to expand its applications while becoming more sustainable and cost-effective. As materials science progresses and digital technologies integrate further with manufacturing, injection molding will likely maintain its position as a cornerstone of modern production.