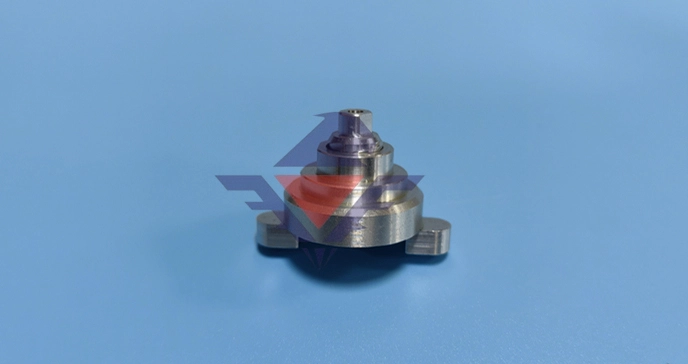
# Swiss Screw Machining: Precision and Efficiency in Small Part Manufacturing
## Introduction to Swiss Screw Machining
Swiss screw machining, also known as Swiss turning or Swiss-type lathe machining, is a specialized manufacturing process that excels in producing small, high-precision components. Originating in Switzerland’s watchmaking industry during the 19th century, this technology has evolved to become a cornerstone of modern precision manufacturing.
## How Swiss Screw Machining Works
Unlike conventional lathes, Swiss screw machines feature a sliding headstock and guide bushing system that provides exceptional stability during machining operations. The workpiece is supported very close to the cutting tool, minimizing deflection and enabling:
– Superior dimensional accuracy
– Exceptional surface finishes
– Tight tolerances (often within ±0.0002 inches)
– Efficient production of complex geometries
## Key Advantages of Swiss Machining
### 1. Precision for Small Parts
Swiss screw machining shines when producing components with diameters typically ranging from 0.5mm to 32mm. The guide bushing system ensures minimal vibration, allowing for precise machining of delicate features.
### 2. High Production Efficiency
Modern CNC Swiss machines can perform multiple operations simultaneously, significantly reducing cycle times. Many machines incorporate live tooling capabilities, enabling milling, drilling, and other secondary operations without removing the part.
### 3. Material Versatility
Swiss machines effectively work with a wide range of materials including:
– Various metals (aluminum, brass, stainless steel, titanium)
– Plastics
– Exotic alloys
## Applications Across Industries
Swiss screw machining serves numerous industries requiring small, precision components:
– Medical devices (surgical instruments, implants)
– Aerospace (fasteners, connectors)
– Electronics (connectors, pins)
– Automotive (fuel injection components)
– Watchmaking and jewelry
## Choosing the Right Swiss Machining Partner
When selecting a Swiss machining service provider, consider:
– Machine capabilities and technology
– Quality control processes
– Material expertise
– Industry-specific experience
– Certifications (ISO, AS9100, etc.)
Keyword: Swiss Screw Machining
## The Future of Swiss Machining
Advancements in Swiss machining technology continue to push boundaries:
– Integration of automation and robotics
– Improved multi-axis capabilities
– Enhanced software for complex programming
– Smart manufacturing with IoT connectivity
As manufacturing demands for smaller, more precise components grow, Swiss screw machining remains at the forefront of meeting these challenges with unparalleled precision and efficiency.