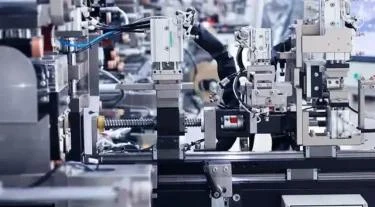
# Tape Production Process and Techniques
## Introduction to Tape Manufacturing
Tape manufacturing is a complex process that involves multiple stages to create adhesive products for various applications. From packaging tapes to medical adhesives, the production techniques have evolved significantly over the years to meet diverse industry requirements.
## Raw Material Selection
The foundation of quality tape production lies in careful raw material selection:
– Backing materials (paper, plastic films, cloth, or foil)
– Adhesive compounds (rubber-based, acrylic, or silicone)
– Release liners and coatings
– Additives for specific properties
## The Tape Production Process
### 1. Backing Material Preparation
The process begins with preparing the backing material, which may involve:
– Unwinding large rolls of film or paper
– Cleaning and treating surfaces
– Applying primer coatings when necessary
### 2. Adhesive Application
Several techniques are used for applying adhesives:
– Solution coating (for solvent-based adhesives)
– Hot melt coating (for thermoplastic adhesives)
– Water-based emulsion coating
– 100% solids coating (UV or electron beam cured)
### 3. Drying and Curing
After application, the adhesive undergoes:
– Solvent evaporation in drying ovens
– Thermal curing for certain adhesive types
– UV or EB curing for radiation-curable adhesives
### 4. Lamination and Winding
The final stages include:
– Applying release coatings if needed
– Laminating multiple layers for specialty tapes
– Precision winding into master rolls
– Quality control inspections
## Advanced Manufacturing Techniques
Modern tape production incorporates several advanced techniques:
### Multi-layer Coating
Allows for combining different adhesive properties in a single tape product.
### Micro-patterned Adhesives
Creates tapes with precisely controlled adhesion characteristics.
### Nanotechnology Applications
Enhances performance through nano-additives in adhesives or backing materials.
## Quality Control Measures
Stringent quality checks ensure consistent tape performance:
– Adhesion strength testing
– Coating weight verification
– Thickness measurements
– Visual inspections for defects
– Aging and environmental resistance tests
## Environmental Considerations
Sustainable manufacturing practices include:
– Solvent recovery systems
– Water-based adhesive formulations
– Recyclable backing materials
– Energy-efficient production methods
## Future Trends in Tape Production
Emerging technologies are shaping the future of tape manufacturing:
– Bio-based adhesives from renewable resources
– Smart tapes with sensing capabilities
– Self-healing adhesive technologies
– Improved recycling and biodegradability
The tape manufacturing industry continues to innovate, developing new products that meet evolving market demands while addressing environmental concerns.
Keyword: tape manufacturing