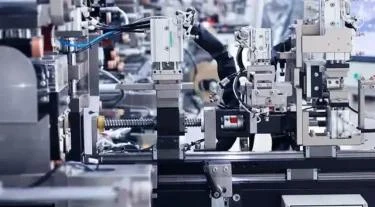
html
Tape Manufacturing: Processes and Innovations
The tape manufacturing industry has evolved significantly over the years, driven by advancements in materials science and production technologies. From adhesive tapes to industrial-grade bonding solutions, the processes involved in tape production are both intricate and fascinating. This article explores the key stages of tape manufacturing and highlights recent innovations shaping the industry.
The Tape Manufacturing Process
Tape manufacturing involves several critical steps to ensure quality, durability, and performance. Below are the primary stages:
1. Material Selection
The first step in tape manufacturing is selecting the right materials. This includes the backing material (such as paper, plastic, or cloth) and the adhesive (acrylic, rubber, or silicone-based). The choice depends on the intended application, whether for packaging, electrical insulation, or medical use.
2. Coating the Backing Material
Once the backing material is chosen, it is coated with the adhesive. This can be done using various methods, including solvent-based, water-based, or hot-melt coating. The coating process must ensure even distribution to avoid weak spots or inconsistencies.
3. Drying and Curing
After coating, the tape passes through drying ovens or UV curing systems to solidify the adhesive. The drying time and temperature are carefully controlled to achieve optimal bonding properties.
4. Slitting and Rewinding
The large rolls of coated tape are then slit into narrower widths and rewound into smaller rolls. Precision slitting ensures clean edges and uniform thickness, which are crucial for performance.
5. Quality Control
Before packaging, the tape undergoes rigorous testing for adhesion strength, tensile properties, and resistance to environmental factors like humidity and temperature.
Innovations in Tape Manufacturing
The tape industry continues to innovate, introducing new materials and processes to meet evolving demands. Some notable advancements include:
Eco-Friendly Tapes
With growing environmental concerns, manufacturers are developing biodegradable and recyclable tapes. These products use plant-based adhesives and sustainable backing materials to reduce environmental impact.
Smart Tapes
Emerging technologies have led to the creation of “smart” tapes with embedded sensors or conductive properties. These tapes are used in electronics, healthcare, and automotive industries for applications like temperature monitoring or electrical conductivity.
High-Performance Adhesives
Advances in adhesive chemistry have resulted in tapes that can withstand extreme conditions, such as high temperatures or heavy loads. These are particularly valuable in aerospace and construction industries.
Conclusion
Tape manufacturing is a dynamic field that blends traditional techniques with cutting-edge innovations. As industries demand more specialized solutions, manufacturers continue to push the boundaries of what tapes can achieve. Whether for everyday use or high-tech applications, the future of tape production looks promising.
Keyword: tape manufacturing