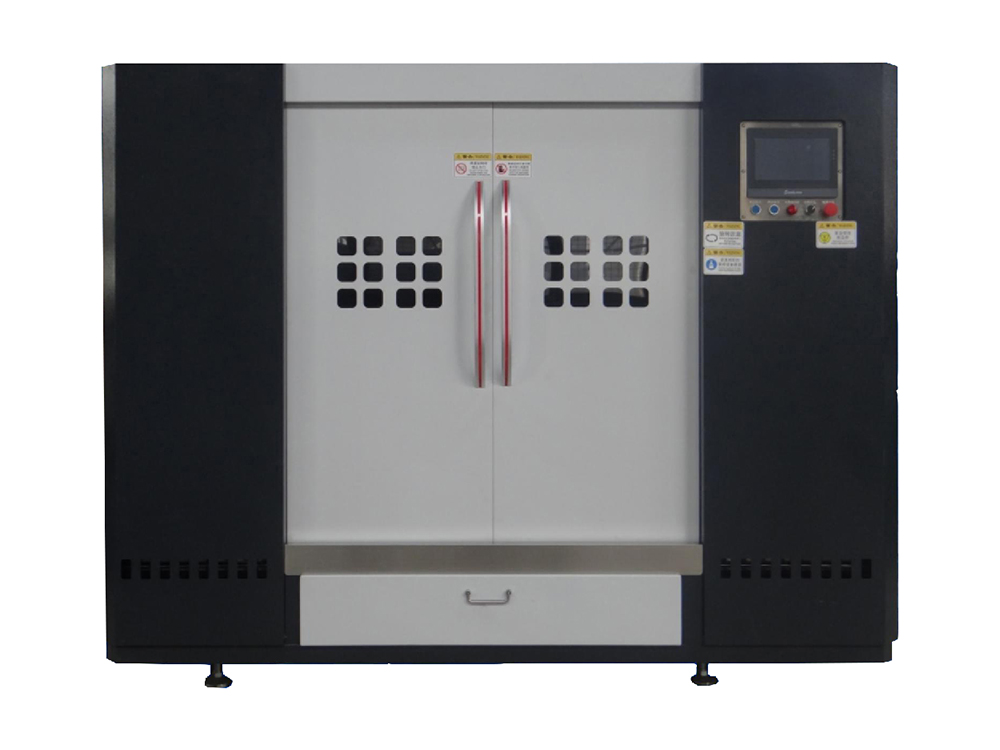
# Dry Polishing Machine for Efficient Surface Finishing
## Introduction to Dry Polishing Machines
Dry polishing machines have revolutionized the surface finishing industry by offering a clean, efficient, and environmentally friendly alternative to traditional wet polishing methods. These machines utilize advanced technology to achieve high-quality finishes without the need for water or other liquids, making them ideal for various industrial applications.
## How Dry Polishing Machines Work
Unlike conventional polishing systems that require water for cooling and lubrication, dry polishing machines operate using specialized abrasives and dust extraction systems. The process involves:
– High-speed rotation of polishing pads
– Effective dust collection mechanisms
– Precise pressure control
– Temperature management systems
This innovative approach eliminates slurry formation and reduces cleanup time while maintaining excellent surface quality.
## Key Advantages of Dry Polishing Technology
The dry polishing method offers numerous benefits over traditional wet polishing:
### Environmental Benefits
– No water consumption
– Reduced chemical usage
– Minimal waste generation
– Lower risk of water pollution
### Operational Efficiency
– Faster processing times
– Reduced cleanup and maintenance
– Continuous operation capability
– Lower overall operating costs
### Quality Improvements
– Consistent surface finishes
– Better control over polishing parameters
– Reduced risk of water spots or staining
– Improved visibility during the polishing process
## Applications Across Industries
Dry polishing machines serve diverse sectors with their versatile capabilities:
### Stone and Concrete Processing
– Marble and granite finishing
– Terrazzo polishing
– Concrete floor preparation
### Metalworking
– Stainless steel finishing
– Aluminum surface treatment
– Automotive component polishing
### Glass Manufacturing
– Edge polishing
– Surface refinement
– Optical glass finishing
## Choosing the Right Dry Polishing Machine
When selecting a dry polishing system, consider these factors:
1. **Material Compatibility**: Ensure the machine is designed for your specific material
2. **Dust Extraction Capacity**: Adequate for your production volume
Keyword: dry polishing machine
3. **Power Requirements**: Matches your facility’s capabilities
4. **Automation Level**: Manual, semi-automatic, or fully automatic options
5. **Maintenance Needs**: Ease of service and part availability
## Maintenance and Safety Considerations
Proper care ensures optimal performance and longevity:
– Regularly clean dust collection systems
– Inspect and replace polishing pads as needed
– Monitor motor performance and temperature
– Follow all safety protocols for dust management
– Provide proper operator training
## The Future of Dry Polishing Technology
As industries continue to prioritize sustainability and efficiency, dry polishing machines are expected to see:
– Advanced dust filtration systems
– Smart monitoring and automation features
– Energy-efficient designs
– Expanded material compatibility
– Integration with Industry 4.0 systems
## Conclusion
Dry polishing machines represent a significant advancement in surface finishing technology, offering environmental benefits, operational efficiencies, and superior quality results. As manufacturing processes evolve toward greener solutions, these systems will play an increasingly important role across multiple industries. By understanding their capabilities and proper implementation, businesses can achieve remarkable surface finishes while reducing their environmental impact and operational costs.