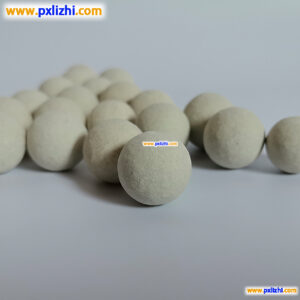
# Ceramic Ball Manufacturing Process and Applications
## Introduction to Ceramic Balls
Ceramic balls are highly specialized spherical components made from advanced ceramic materials. These precision-engineered spheres offer exceptional properties that make them invaluable in various industrial applications. Their unique characteristics stem from the manufacturing process and the ceramic materials used in their production.
## The Manufacturing Process of Ceramic Balls
### 1. Raw Material Selection
The production of ceramic balls begins with the careful selection of raw materials. Common ceramic materials used include:
– Alumina (Al2O3)
– Zirconia (ZrO2)
– Silicon nitride (Si3N4)
– Silicon carbide (SiC)
Keyword: ceramic ball
The choice of material depends on the intended application and required properties such as hardness, wear resistance, and thermal stability.
### 2. Powder Preparation
The selected ceramic powder undergoes several preparation steps:
– Milling to achieve uniform particle size
– Mixing with binders and additives
– Homogenization to ensure consistent composition
### 3. Forming Process
There are several methods to form ceramic balls:
#### Isostatic Pressing
Cold isostatic pressing (CIP) applies uniform pressure from all directions to form spherical shapes with high density and uniformity.
#### Extrusion and Spheroidization
For smaller diameter balls, ceramic paste is extruded and cut into small pieces that are then rolled into spherical shapes.
#### Injection Molding
This method is suitable for complex shapes and high-volume production, where ceramic powder is mixed with thermoplastic binders and injected into molds.
### 4. Sintering
The formed green balls undergo sintering in high-temperature furnaces:
– Temperature typically ranges from 1400°C to 1800°C
– Process duration varies from several hours to days
– Controlled atmosphere (air, vacuum, or specific gas) depending on material
### 5. Precision Grinding and Polishing
After sintering, ceramic balls undergo precision finishing:
– Diamond grinding to achieve exact dimensions
– Lapping for surface refinement
– Polishing to reach required surface finish and sphericity
### 6. Quality Control
Each ceramic ball undergoes rigorous inspection:
– Dimensional accuracy measurement
– Surface quality assessment
– Mechanical property testing
– Batch consistency verification
## Applications of Ceramic Balls
### Bearings
Ceramic balls are widely used in high-performance bearings due to their:
– Excellent wear resistance
– High stiffness
– Corrosion resistance
– Light weight compared to steel
Common applications include aerospace, medical equipment, and high-speed machinery.
### Valves and Pumps
In fluid handling systems, ceramic balls serve as:
– Check valve components
– Metering elements
– Pump bearings
– Sealing components
Their chemical inertness makes them ideal for corrosive environments.
### Grinding Media
Ceramic balls are excellent grinding media for:
– Paint and pigment production
– Pharmaceutical processing
– Food industry applications
– Mineral processing
They offer contamination-free grinding with high efficiency.
### Other Specialized Applications
– Ball screws in precision machinery
– Measuring instruments
– Semiconductor manufacturing equipment
– Spacecraft components
– Dental and medical implants
## Advantages of Ceramic Balls
The unique properties of ceramic balls provide numerous advantages:
– High hardness and wear resistance
– Excellent corrosion resistance
– Low density (40-60% of steel)
– High temperature capability
– Electrical insulation properties
– Non-magnetic characteristics
– Long service life in demanding environments
## Future Trends in Ceramic Ball Technology
The ceramic ball industry continues to evolve with:
– Development of new ceramic compositions
– Improved manufacturing techniques for higher precision
– Nanostructured ceramics for enhanced properties
– Larger diameter balls for industrial applications
– Cost reduction through optimized production methods
As technology advances, ceramic balls will find even broader applications across various industries, pushing the boundaries of performance in extreme operating conditions.