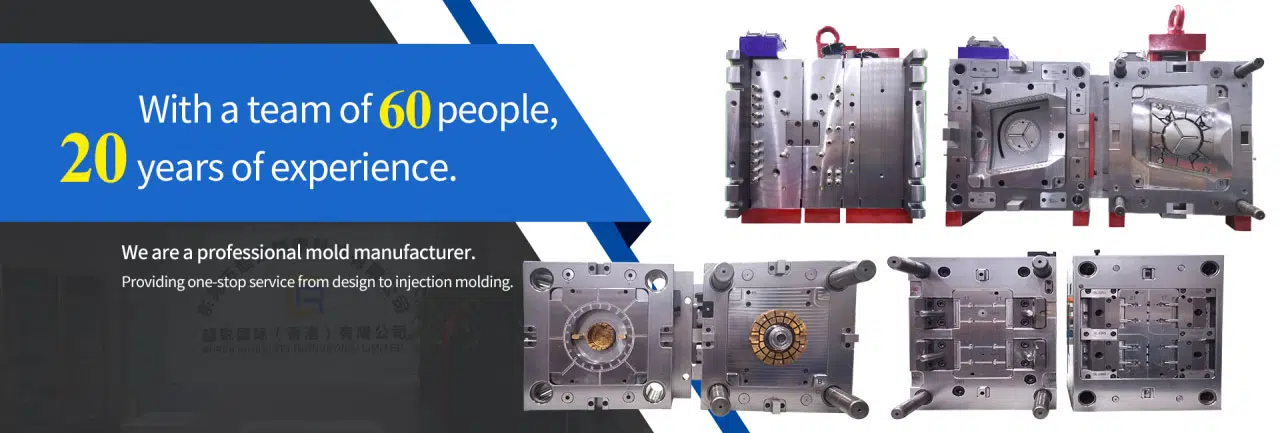
# Vacuum Casting Technology in Modern Manufacturing
## Introduction to Vacuum Casting
Vacuum casting is a versatile manufacturing process that has gained significant popularity in modern production environments. This technique combines the precision of traditional casting methods with advanced vacuum technology to create high-quality parts with excellent surface finish and dimensional accuracy.
## How Vacuum Casting Works
The vacuum casting process begins with creating a master pattern, typically using CNC machining or 3D printing. This pattern is then used to make a silicone mold under vacuum conditions to eliminate air bubbles and ensure perfect replication of the original design.
Once the mold is prepared, liquid polyurethane or other casting materials are poured into the mold cavity while maintaining vacuum pressure. This vacuum environment helps the material flow into all intricate details of the mold without trapping air, resulting in defect-free castings.
## Advantages of Vacuum Casting Technology
### High Precision and Detail Reproduction
Vacuum casting excels at reproducing fine details and complex geometries that would be challenging with other manufacturing methods. The vacuum environment ensures complete material penetration into all mold features.
### Cost-Effective for Small Batch Production
Compared to injection molding, vacuum casting offers a more economical solution for producing small quantities of parts (typically 10-50 units) without the need for expensive metal tooling.
### Material Versatility
Modern vacuum casting systems can work with various materials that mimic the properties of engineering plastics, rubber-like materials, and even transparent resins, providing designers with multiple options for their prototypes or end-use parts.
### Rapid Turnaround Times
The relatively simple tooling process allows for quick production cycles, making vacuum casting ideal for rapid prototyping and bridge manufacturing between prototyping and full-scale production.
## Applications in Various Industries
Vacuum casting technology finds applications across multiple sectors:
– Automotive: For prototyping interior components, gaskets, and functional parts
– Medical: Creating anatomical models and device prototypes
– Consumer Electronics: Housing prototypes and functional testing models
– Aerospace: Lightweight component development
– Industrial Design: Product concept validation and presentation models
## Future Developments in Vacuum Casting
As manufacturing demands evolve, vacuum casting technology continues to advance. Emerging trends include:
– Development of new casting materials with enhanced mechanical properties
– Integration with digital manufacturing workflows
– Improved automation in the casting process
– Hybrid approaches combining vacuum casting with other manufacturing techniques
These innovations promise to further expand the capabilities and applications of vacuum casting in modern manufacturing environments.
## Conclusion
Keyword: Vacuum Casting
Vacuum casting has established itself as a valuable manufacturing solution that bridges the gap between prototyping and mass production. Its ability to produce high-quality parts quickly and cost-effectively makes it an essential tool for product developers and manufacturers across various industries. As technology advances, we can expect vacuum casting to play an even more significant role in the future of manufacturing.